Design for the Environment/Internal Combustion Engines
This page is part of the Design for the Environment course

In a world of relentless technological advancement, our resources are subjected to the inverse effect of a continuous, steady decline; our limited and diminishing resources stand as a roadblock in the promise of a progressive and sustainable future. They prove to be an ever increasing worry as energy demands constantly surface due to the development of countries like China or India, with billions in population. The automotive industry is inherently correlated to the economic development of such countries, and plays a major role in global energy consumption. Thus materializes this study and its purpose.
The objective of this study is to compare two potential alternatives, E85 Ethanol-Gasoline and Hydrogen, against Gasoline as a source of fuel in automotive vehicles. In order to conduct this study in a fair and comparative manner, we draw the system boundary around the fuels and its required modifications to function in an Internal Combustion Engine. In each life stage of the fuels, we perform a thorough functional, economic, environmental, costs and societal analysis analysis; thus allowing for a comprehensive evaluation of each fuel’s overall impact, and setting the stage to select the ideal alternative.
Gasoline boasts the highest energy efficiency and mileage, and is employed as the primary source of fuel today. Infrastructure for the production and transportation of gasoline is highly developed, as it has been in constant refinement for over 60 years. However, it is a heavy consumer of our limited natural resources and is also a major contributor of greenhouse gases. Thus it raises the need for alternative fuels, that rely on renewable resources and have lower emissions during its lifecycle.
Ethanol is derived from corn and is highly corrosive; thus it cannot be transported through pipelines and requires vehicular transportation. Production of ethanol is an energy-intensive process but offers low environmental emissions for the IC engine during its use phase. Ethanol-Enriched fuel (E85) is cheaper than gasoline, but has a lower mileage at 14 mpg. Hence, it requires more regular refilling that accumulates to be more expensive in the long run.
Hydrogen fuel offers a gradual transition into the event of a heavy global dependence on alternative fuels. Hydrogen can be produced using existing infrastructure and H2ICEs can be supplemented with gasoline when a hydrogen fuelling station is not available. It can be produced through a wide range of sources and offers zero (negligible) harmful emissions during its use phase. However, it has a mediocre mileage at 4.2mpg and the production of hydrogen is an energy-intensive process.
This report and its results are to be proposed to Toyota, to aid in implementing an environmentally friendly – yet cost-effective – internal combustion engine.
Project Information
[edit | edit source]Section 1 Group 3A
Wong, Timothy (Timdy.wong)
Mohabir, Christopher (Mohabir)
Zahedi, Elyad (Elyad,zahedi)
Chotai, Tejas (Tejas)
Highlights and Recommendations
[edit | edit source]When constantly utilized on a global scale, it is imperative that the fuel of choice has the least total harmful emissions throughout its life cycle – especially during its use phase. Hydrogen offers negligible emissions throughout its use phase, but current technology prohibits it from being implemented on a global scale; this is due to its large energy consumption during its manufacturing stage. Hydrogen has the potential to solve our environmental and energy crisis because of its low emissions and its different possible sources of production. Hence, Hydrogen is the preferred design alternative.
A further streamlined, economic input-output and societal analyses of the results weighs Hydrogen and Ethanol-Gasoline relative to the baseline – Gasoline. The following table is attained by a summation of GWPS from the EIOLCA, integrated with essential results from the Functional, Costs, and Streamlined Lifecycle Analysis.
The EIOLCA, rates E85 to be the best fuel with the lowest GWP emissions, and Hydrogen rated a close second. However, it should be taken into account that the use stage of a product results in the highest total GWP and GHG emissions. During the use phase of Hydrogen, there are zero emissions; the resulting emissions for hydrogen result solely from the infrastructure requirements in the pre-manufacturing and manufacturing life stages. Conversly, E85 emits a total of 37,960 MTCO2 (75.6% of the total) during its use phase. Thus, if the manufacturing processes of hydrogen is more energy efficient, Hydrogen has the greatest potential to solve our environmental crisis.
The Functional Analysis, rates Gasoline to be the most practical with a high mileage of 23.3mpg. Accordingly, the average consumer (30,000km/year) would have to refill the fuel tank approximately once every 12, 7 and 5 days for Gasoline, E85 and H2ICE respectively. If hydrogen is implemented, it is a slight deterrent to refill once every five days, but it offers the public an option to do their part for a sustainable future.
In the Costs Analysis, E85 is the most expensive to sustain, which is mainly attributed to the direct costs in its use phase. Costs of fuel throughout the average 16.1 year lifespan of a vehicle are $34845.56 $41677.3 $36162.5 for Gasoline, E85 and Hydrogen respectively. As should be noted, the price for a consumer to purchase hydrogen fuel is relatively similar to that of gasoline.
The Societal Analysis of the fuels all differ significantly, and determining which has the greatest impact would be soley based on subjective reasoning. However, Hydrogen differs only slightly from gasoline, where the main concern is its safety. Like gasoline, hydrogen is prone to exploding if not handled carefully. More improvements in the safety of implementing hydrogen as a fuel would have to be considered.
By a slim margin, the results of the Streamlined Lifecycle Analysis show that Gasoline is the fuel of choice. However, the SLCA weighs the importance of each life stage equivalently, which cannot be the case in a real world scenario. The environmentally-harmful emissions in each life stage differ greatly, and so life stages should be proportionally levied to account for this. If such were the case, and the use phase of the product were weighed to be of higher significance, Hydrogen fuel would have been the clear winner.
Streamlined Life Cycle Assessment
[edit | edit source]Gasoline IC Engine
[edit | edit source]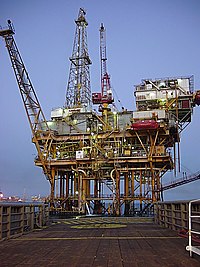
The following streamlined life cycle analysis outlines the environmental impacts associated with the life cycle stages of a BMW 325i 2996 ccm petrol (gasoline) ICE.
Petrol
Petrol is derived from crude oil or petroleum, which is of finite supply and requires energy
intensive extraction strategies[1]. This extraction process requires the implementation of a pump system that is powered by the combustion of coal, resulting in large quantities of GHG emissions. The refinement of petroleum is carried out in distillation towers and is separated from the raw petroleum at a relatively low temperature of 150 degrees Celsius[2]. Bi-products associated with this refinement process consist primarily of coke, light cycle oil, heavy fuel oil and wastewater. All of these residues, with the exception of wastewater, are used as material inputs for other products[3]. The transportation of petrol is achieved primarily through the means of pipelines. In comparison to the alternative fuels, this form of transport is superior in terms of cost effectiveness and efficiency.
Gasoline ICE & Fuel Tank
The gasoline ICE is composed primarily of virgin iron, steel and aluminium [4], whereas the fuel tank is composed of HDPE[5]. HDPE is a superior material choice, requiring relatively fewer energy instensive production processes for its production. Manufacturing the fuel tank, by means of blow molding, requires relatively low levels of heat ranging from 180 to 220 degrees Celsius[6]. The overall recylability of gasoline ICEs and HDPE fuel tanks are generally high as reflected by the EU Directive, (2005/64/EU), stating at least 85 percent of new vehicles are capable of being recycled by December 2008. There are, however, various negative aspects associated with the selection of petrol and HDPE as primary material inputs. Both petrol and the HDPE fuel tank are derived from petroleum which is of finite supply that contains hazardous substances. The performance aspect of gasoline ICE is a positive point. The 325i has CO2 emission levels of 170g/km and fuel consumption rates of 9.8l/km (urban)[7], reflecting efficient levels of energy consumption. Solid residues associated with the use phase of the gasoline ICE and HDPE fuel tank are relatively low. Liquid residues include motor oil which is routinely changed. A significant disadvantage of gasoline ICEs include the quantity of hazardous gases are emitted from the combustion of petrol.
Ethanol-Gasoline Flex-fuel Engine
[edit | edit source]For an ethanol-enriched fuel, such as E85, the portion of gasoline to ethanol is considerably low. Thus, in scoring processes, the factors related to gasoline are relatively weighted less than those of ethanol. Note that details are not given for factors considered negligible.
Ethanol-Enriched Fuel
The main resource used in North America to produce ethanol is from corn farms. The energy consumed in farming corn in order to produce 1 liter of ethanol is about 7,440 KJ. [8] Farmers fertilize corn fields with nitrogenbased compounds. The fertilizer run-off flows down rivers into lakes, making algae bloom on the surface, cutting oxygen to creatures that live on the bottom. [9] In total, producing 1 liter of ethanol through dry-milling process requires about 12,350 KJ. Dried distillers grains with solubles (DDGS) and CO2 are formed during this process. DDGS is a common livestock feed and carbon dioxide is captured and sold for use in carbonated beverages and dry ice manufacturing. Ethanol is a highly corrosive substance. Ethanol, once produced, is blended with about 5% denaturant (such as gasoline) to make it undrinkable so as to avoid beverage alcohol taxes. [10] Even this mixture cannot be transported using pipelines due to corrosive characteristic of ethanol. Therefore large tanks that are resistive to corrosion are filled with ethanol-enriched fuel. These tanks are then transported to retailers using barges, trains and trucks.
Ethanol FFV ICE & Fuel Tank
Primary materials used in ICE are iron and steel. These materials require high levels of energy
for extraction and smelting processes (Ranging from 20 to 342 MJ/KG). [11] The extraction of metal ore involves producing solid residues such as waste rocks and liquid residues due to mine drainage. [12] Stainless steel is an iron-carbon alloy with a minimum of 11.5 wt% chromium content. [13] Chromium is considered to be a scarce material and thus is a poor material choice. [14]Polymer production results in a high energy use due to use of high-power water jets. [15]Packaging and transportation for all engines involve similar procedures. However in the case of FFVs, larger and heavier fuel tanks should be considered. Ethanol reduces tailpipe carbon monoxide emissions approximately 30%, toxics content by about 34%, and tailpipe fine particulate matter (PM) emissions by 50%, when compared to regular gasoline engine.[16] Materials used in engines are mostly metals, which are recyclable substances. Teflon recycling involves a less energy intensive method. It’s heated to elevate its temperature and then it’s extruded to form pellets that can be sent back to factory for assembling. [17]
Hydrogen IC Engine
[edit | edit source]The following is the streamlined life cycle analysis for Hydrogen Internal Combustion Enigne
(H2ICE) and for the resource extraction, manufacturing, and transportation of Liquid Hydrogen
(LH2).
Liquid Hydrogen
The two main materials required for hydrogen production via Steam Methane Reforming are water for steam generation and natural gas, a limited resource, for producing mathane gas feedstock [18]. Extraction of naturalgas is a energy intensive procedure powered by coal combustion [19].Manufacturing stage includes multiple processes, mainly SMR, carbon sequestration and hydroden liquidification. SMR reaction yields a gaseous mixture of hydrogen and carbon dioxide at 700-1000 degrees celcius[20]. Then, hydrogen gas is cooled into its liquid state and stored [21]; whereas, the resulting carbon dioxides are collected, compressed and injected into underground [22].One disadvantage of LH2 over a compressed hydrogen gas is that it can not be carried using pipeline because it must be stored at a cryogenic temperature, thus trucks and ships must be used for LH2 distribution [23].Furthermore, since volumtetric energy density of an liquid hydrogen is a quater of gasoline, LH2 four-times the volume of gasoline must be transported to deliver equivalent energy content.
Hydrogen ICE & LH2 Fuel Tank
Primary materials used for engine manufacturing is stainless steel (specifically, X2 CrNi 19 11) for the LH2 fuel tank and cast iron for the engine block [24]. Both of these materials are ferrous metals meaning large amount of wastes are produced from the iron mining.In addition, stainless steel includes significant amount of chromium, which is a scarce material.However, most of these metals are highly recyclable materials and so this design minimizes solid wastes at the end-of-life stage.Manufacturing of the LH2 fuel tank is energy inefficient process. This is because the tank requires high-accuracy manufacturing and it can not be produced in large volume [25]. Regarding the the product delivery, since the fuel tank for Hydrogen vehicle is larger than other alternatives due to low volumetric energy energy density of the fuel, the transportation phase produces correspondingly larger emissions and packaging wastes.However, the main advantage of hydrogen vehicle lies in its use phase. BMW Hydrogen 7 is a near-zero emission vehicle, thus produces significantly low amount of harmful gases when driving on hydrogen.
Economic Input Output Life Cycle Assessment
[edit | edit source]An economic input-output life cycle analysis allows for a quantitative analysis of environmental impacts in all life stages of each alternative. The EIOLCA tool was used to conduct this study. This assessment is performed for the pre-manufacturing, manufacturing and use life stages of the car. Assuming 185,000 miles covered for the total life span of the car, the life stage that has the most impact is the use phase; the most amount of emissions is emitted and a considerable amount of energy is consumed. Regarding the recycling life stage, most components used in cars are re-usable and the metal components are recyclable. Along with the fact that this life stage is very similar for all three fuels and thus insignificant for a comparison analysis, it is not considered in the EIOLCA. Energy consumption and GWP data for baseline and two alternatives are shown below.
The graphs above show that for Gasoline, the highest emissions are attributed to the use phase of the product. E85 has a lower emission level during its use phase, whereas Hydrogen Fuel has negligible amounts of emissions. Overall, Hydrogen emits the least GWP emissions, but consumes the most energy. It should be noted that the negative effects of hydrogen -high energy consumption and GWP emissions- are mainly attributed to the production phase of the fuel. In due time, technological advances could aid in reducing the pollution and energy consumption of the production of Hydrogen. It offers the ideal amount of emissions, none, during its use phase; thus Hydrogen has the highest potential to solve our environmental crisis.
Costs Analysis
[edit | edit source]Gasoline IC Engine
[edit | edit source]Material costs for this analysis includes only the engine/fuel tank component as the fuel costs were accounted for when determining the operation cost of the product. The cost of the engine/fuel tank is determined to be $387.96[26].
Significant differences in labour, maintenance and operational costs are primarily influenced by the fuel aspect. For comparative purposes the labour costs associated with the engine component are therefore neglected. Assuming mileage is 70% urban and 30% highway, fuel costs are calculated for one year (11 562miles). These costs were determined to be $1 454.06[27] and reflect the operation costs of the product. The total direct costs where then found[28][29][30]:
Direct Costs = $34 845.56
Conventional gasoline ICE’s are primarily GHG contributors, as such, the health costs associated with only these emissions will be determined. Health costs induced by GHG emissions are extrapolated by employing data related to total health costs incurred from air pollution and total GHG emissions. This analysis will therefore take into account the pre-manufacturing, manufacturing and use stages of the lifecycle of a gasoline ICE. Health costs generated by GHG emissions were calculated in terms of the indirect cost per unit of the product. This was determined as follows:
Total Health Cost[31] / Amount of GHG Emissions[32] = 8.8 $/metric tonnes CO2 equivalent
Carbon dioxide emissions are found for all the stages in the form of global warming potential using the economic input-output life cycle analysis:
Total GWP = 71.64 MTCO2
Therefore the indirect cost for green house gases emissions is determined to be
Indirect Costs = 70.64* 8.8 = $631.86
Ethanol-Gasoline Flex-fuel Engine
[edit | edit source]Since the mass of Teflon polymer used in the engine is negligible in comparison to other
materials, its cost is neglected. Also, since the labour, manufacturing processes and maintenance for engines are similar for each alternative, their cost analysis is not necessary. For operation costs, since the fuel consumption is different for each alternative, the total cost of fuel over life span of the car is calculated. Supposing that a car lasts for 16 years, it would be driven about 11,562 miles per year. Assuming 70% city mileage, 30% highway mileage and E85 price of $2.55 [33], the fuel cost for one year is determined to be
Direct Costs = $41,677.3
Since the magnitude of toxic releases and air pollutants are less significant than that of greenhouse gas emission, indirect costs are determined based on Global Warming Potential. First, the indirect costs associated with GHG emissions are determined using the ratio between total estimated health costs and the total amount of GHG released in California in a year. [34] This factor integrates the economic cost associated with health care and it’s calculated as follows:
Total Health Cost / Amount of GHG Emissions = 8.8 $/metric tonnes CO2 equivalent
Carbon dioxide emissions are found for all the stages in the form of global warming potential using the economic input-output life cycle analysis:
Total GWP = 50.24 MTCO2
Therefore the indirect cost for green house gases emissions is determined to be
Indirect Costs = 50.24 * 8.8 = $442.11
Sensitivity Analysis
[edit | edit source]The method used to produce ethanol has been improving in the past couple of decades to reduce the amount of energy consumption. The dry-milling process, consumed about 70,000 Btu to produce a gallon of ethanol in 1980’s. Recently, this amount of energy has dropped to 40,000 Btu per gallon due to advances in technology. [35]Assuming this trend would continue for the next couple of decades, the energy associated with production of ethanol would reduce by almost 40%. This would affect the costs by a large factor and make ethanol-enriched fuels more affordable. Furthermore, the price of gasoline is depended on the crude oil prices, which fluctuate significantly and has been rising due to current events in Middle-East. The continuous ascend in price of gasoline in near future will affect the cost analysis of ethanol-enriched fuel and it will increase the demand for ethanol.
Hydrogen IC Engine
[edit | edit source]As mentioned earlier, 200kg of weight was added to the vehicle when BMW 760i was modified to operate on hydrogen fuel. The cost analysis below was performed under assumption that this 200kg is the mass of the hydrogen fuel tank, primarily from the stainless steel. Hence, the material costs for the engine and fuel tank component were found by adding 200kg of stainless steel to the model used in Gasoline ICE section.cost was found to be $1123.54.
Average lifetime of the hydrogen vehicle is assumed to be total of 185000miles over the span of 16years,so average
miles traveled each year will be 11562miles. LH2 fuel cost for current steam methane reforming technology is
estimated to be $2.17 /kg [36]. Therefore annual fuel cost can be calculated as $1605.51. Therefore, with the annual compund rate of 4%, the total direct cost of hydrogen ICE over its lifetime is determined to be:
Direct Costs = $36162.51
The indirect cost for the hydrogen vehicle was found in the same manner as for other two alternatives. However, the total emmisions produced over the life-cycle of this product was found, using the economic input-output life cycle analysis, to be:
Total GWP = 56.631 MTCO2E/Unit H2ICE
Therefore the indirect cost for the green house gas emmision is determined to be:
Indirect Costs = 56.631 MTCO2E * $8.8/MTCO2E = $499.49
Sensitivity Analysis
[edit | edit source]It was stated earlier that the hydrogen is produced at a central station plant, large enough to provide
up to 2million hydrogen vehicles [37]. In approximately a decade, the cost of hydrogen has the potential
to be reduced to $1.72/kg H2 using the same natural gas reforming method. However, the following
conditions must apply[38]:
· Central Station is operated at full capacity [39].
· Efficiency of SMR process is increased to 68% from current 61% efficiency [40].
· Reduction GHG emissions from power generation sector, meaning more renewable energy generated
[41].
If price of hydrogen was lowered to $1.72/kg H2 then the fuel cost for lifetime of one vehicle will be
$27773.24 (as opposed to the present cost of $35039.50), which is lower than the cost of gasoline per vehicle. Note that this value was calculated using
same method as operation cost calculated earlier.
Societal Analysis
[edit | edit source]Gasoline IC Engine
[edit | edit source]Gasoline is coming under increased scrutiny as interest in alternative fuels and engine developments continually grow. There are a number of incentives for the exploration of a potential successor to petroleum fuels. One of which is the increasing scarcity of crude oil, which has caused steep climbs in North American gas prices. The volatility of these prices has also caused considerable frustration as seemingly bizarre price hikes are justified by conflicts in major oil producing regions such as the Middle East. More recently, society’s awareness of greener alternatives has greatly expanded as exemplified by events such as Earth Hour. This push for environmentally friendly technologies will make the gasoline ICE progressively more irrelevant, as society better understands the negative environmental impact that it generates. The advantages of the gasoline ICE lie in the heavily developed infrastructure surrounding its production. Petroleum refinement has been in major development since 1875 and transport of the fuel was made efficient by investing billions of dollars in pipelines. Rapidly industrializing nations such as China and India have committed to investments in pipeline development and are therefore obligated to maximize their use and in turn maximize profits.
Ethanol-Gasoline Flex-fuel Engine
[edit | edit source]Fluctuating oil prices, a country’s dependency on foreign oil, global warming threats and the government’s support for alternative fuels all have an influence on people’s preferences of fuel. However, cost is the main and sometimes the only factor. For some, environmental impacts play a greater role. As discussed, the fuel cost for the whole life of a vehicle is more for E85. But clearly, production of FFV’s by car manufacturers has been increasing because of increase in demand for ethanol-enriched fuel as a substitution for gasoline in order to reduce the environmental effects and not because of its lower prices. [42]As the use of alternative fuels increase, the dependency on oil decreases. On the other hand, as the demand for ethanol increases, the need for imported crops rises too. Since ethanol can be produced from renewable sources, it is considered to be a more reliable import good because of the consistency in price. Thus, people would feel safer in terms of long-term financial planning.
Hydrogen IC Engine
[edit | edit source]One of the biggest societal concern regarding hydrogen is the safety issue. Hydrogen is both explosive and flammable just like gasoline. Moreover, “hydrogen/air mixture requires relatively little energy to ignite and remains ignitable at broad mixture range [43].” Following mechanical requirements must be met to ensure safety of the passengers:
· No significant amount of hydrogen must escape from the storage tank [43].
· Cold burns from cryogenic liquids must be prevented [43].
· Ignitable hydrogen/air mixture must not form, especially in closed spaces such as garages [43].
In general, when hydrogen is carried on-board, special caution must be taken for the cryogenic
fuel tank because it is the most vulnerable component in the hydrogen vehicles.
References
[edit | edit source]- ↑ Thomas Graedel. Streamlined Life-Cycle Assesment. New Haven USA: Prentice Hall, 1998.
- ↑ Australian Institute of Petroleum. “PETROLEUM TOPIC FACT SHEET.” Date of Access: 30 March 2008
- ↑ Craig C. Freudenrich. “How Oil Refining Works.” Date of Access: 30 March 2008 http://science.howstuffworks.com/oil-refining5.htm
- ↑ BMW. “2006 BMW 325i.” Date of Access: 30 March 2008 http://www.conceptcarz.com/vehicle/z10521/BMW_325i.aspx
- ↑ Chris T. Hendrickson. “Environmental Life Cycle Assessment of Goods and Services: An Input- Output Approach.” : RFF Press, 2006
- ↑ MatWeb. “Total Finathene® 3802 HDPE, blow molding, cable.” Date of Access: 30 March 2008 http://www.matweb.com/search/datasheettext.aspx?matid=38634
- ↑ BMW. “BMW 3 Series Sedan: Technical Data.” Date of Access: 30 March 2008 http://www.bmw.com/com/en/newvehicles/3series/sedan/2005/allfacts/engine_data.html
- ↑ Renewable Fuel Association. “How ethanol is made.” Date of Access: 26 March 2008 http://www.ethanolrfa.org/resource/made/
- ↑ Zabarenko. “Corn-Based Ethanol Could Worsen the Dead Zone.” Date of Access: 17 March 2008 http://uk.reuters.com/article/email/idUKN1048003520080311
- ↑ Renewable Fuel Association. “Ethanol Facts.” Date of Access: 26 March 2008 http://www.ethanolrfa.org/resource/facts/
- ↑ BMW. “2006 BMW 325i.” Date of Access: 30 March 2008 http://www.conceptcarz.com/vehicle/z10521/BMW_325i.aspx
- ↑ William S. Pretzer. “Iron Background.” Date of Access: 30 March 2008 http://www.madehow.com/Volume-2/Iron.html
- ↑ American Iron and Steel Institute. “Steel Glossary.” Date of Access: 26 March 2008 http://www.steel.org/AM/Template.cfm?Section=Statistics
- ↑ Thomas Graedel. Streamlined Life-Cycle Assesment. New Haven USA: Prentice Hall, 1998.
- ↑ University of Utah Engineering. “Polytetrafluoroethylene.” Date of Access: 23 March 2008 http://www.eng.utah.edu/~nairn/mse/students/MSE3410/Teflon/Recycling.html
- ↑ Office of Sustainable Development of Portland “Biofuels and Emissions.” Date of Access: 28 March 2008 http://www.portlandonline.com/osd/index.cfm?a=bcddfc&c=ecied
- ↑ Cambridge University Engineering Department. “Energy to Cost.” Date of Access: 21 March 2008 http://www-materials.eng.cam.ac.uk/mpsite/interactive_charts/energy-cost/IEChart.html
- ↑ Hydrogen Production.2005.20 March 2008<http://www.hydrogentrade.com/production/>
- ↑ Natural Gas from Coal.2008. Husky Energy. 27 March 2008 <http://www.huskyenergy.ca/operations/westerncanadaconventionaloilandgas/crudeoil&naturalgasdevel opment.asp>
- ↑ Cutler J. Cleveland. Hydrogen Production Technology. 2007. The encyclopedia of earth. 20 March 2008 <http://www.eoearth.org/article/Hydrogen_production_technology#Steam_Methane_Reforming>
- ↑ Prospects for Hydrogen and Fuel Cells. Ed. International Energy Agency. Paris, France: International Energy Agency, 2005.
- ↑ Technologies: Carbon Sequestration. National Energy Technology Laboratory. 27 March 2008 <http://www.netl.doe.gov/technologies/carbon_seq/index.html>
- ↑ Prospects for Hydrogen and Fuel Cells. Ed. International Energy Agency. Paris, France: International Energy Agency, 2005.
- ↑ Hydrogen IC Engines. Ed. SAE World Congress. Warrendale, PA: Society of Automotive Engineers, 2006.
- ↑ Hydrogen IC Engines. Ed. SAE World Congress. Warrendale, PA: Society of Automotive Engineers, 2006.
- ↑ Kamalideen Rahaman, Chris Mohabir, Personal Interview 905-426-1531, Wednesday 12th March 2008, 2260 Battleford Road, Chrysler Toronto, Ontario
- ↑ Financial Forecast Center. “U.S. Inflation Rate Forecast.” Date of Access: 30 March 2008
- ↑ Van Basshuysen, Richard. “Internal combustion engine handbook : basics, components, systems, and perspectives.” Warrendale, PA : SAE International, 2004.
- ↑ ROYMECH. “Metal Costs.” Date of Access: 30 March 2008 http://www.roymech.co.uk/Useful_Tables/Matter/Costs.html
- ↑ ROYMECH. “Plastics Costs.” Date of Access: 30 March 2008
- ↑ Environmental Protection. “Economic Analysis Measures Air Pollution Costs To California Region.” Date of Access: 30 March 2008
- ↑ ClimateChange. “Energy.” Date of Access: 30 March 2008
- ↑ U.S Department of Energy “AFDC: Vehicles.” Date of Access: 26 March 2008 http://www.eere.energy.gov/afdc/progs/cost_anal.php
- ↑ Environmental Protection. “Economic Analysis Measures Air Pollution Costs To California Region.” Date of Access: 30 March 2008 http://www.eponline.com/articles/53958/
- ↑ Wang. “Energy and GHG Emissions.” Date of Access: 21 March 2008 http://www.ethanolrfa.org/objects/documents/981/energy_and_ghg_emissions_-_wang_2005.pdf
- ↑ The Hydrogen Economy : Opportunities, Costs, Barriers, and R&D Needs. Ed. National Research Council (U.S.)., National Academy of Engineering., and National Academy of Sciences (U.S.). Washington, D.C.: National Academies Press, 2004.
- ↑ The Hydrogen Economy : Opportunities, Costs, Barriers, and R&D Needs. Ed. National Research Council (U.S.)., National Academy of Engineering., and National Academy of Sciences (U.S.). Washington, D.C.: National Academies Press, 2004.
- ↑ The Hydrogen Economy : Opportunities, Costs, Barriers, and R&D Needs. Ed. National Research Council (U.S.)., National Academy of Engineering., and National Academy of Sciences (U.S.). Washington, D.C.: National Academies Press, 2004.
- ↑ The Hydrogen Economy : Opportunities, Costs, Barriers, and R&D Needs. Ed. National Research Council (U.S.)., National Academy of Engineering., and National Academy of Sciences (U.S.). Washington, D.C.: National Academies Press, 2004.
- ↑ The Hydrogen Economy : Opportunities, Costs, Barriers, and R&D Needs. Ed. National Research Council (U.S.)., National Academy of Engineering., and National Academy of Sciences (U.S.). Washington, D.C.: National Academies Press, 2004.
- ↑ The Hydrogen Economy : Opportunities, Costs, Barriers, and R&D Needs. Ed. National Research Council (U.S.)., National Academy of Engineering., and National Academy of Sciences (U.S.). Washington, D.C.: National Academies Press, 2004.
- ↑ California Energy Commission. “E85 FFV Availibilty” Date of Access: 2 March 2008 http://www.energy.ca.gov/afvs/documents/2004-10-12_ETHANOL.PDF